Metal Fabrication in 5 Steps
How to Manufacture Metal Fabrication Parts
To really learn about manufacturing metal fabrication parts, you should have a general understanding of what metal fabrication is. Metal fabrication involves taking a metal material of some form, sheets plate, bar, angle, structural or some other form of metal and fabricating or forming them conform to a specific shape. Almost everywhere you look today, you will see metal fabrications used for almost everything you can imagine. The car you drive, the phone you answer, or the electronic equipment you use, the building you work in or shop in, all are likely candidates for the use of metal fabrication.
If you enter into the fabrication process with even a little more knowledge of some of the various materials and methods used in metal fabrication, you increase the likelihood of your project’s success. You will also be much more confident in working through the process and you will have a better chance of keeping your costs lower without sacrificing quality. This article is not meant to be all inclusive, but rather it is a primer for someone to get enough information to have a better sense of the steps they need to take, and general processes that can be followed to help you improve your odds of achieving your goals. Metal fabrication is a complicated process, requiring extensive knowledge and research. This is why we have created this guide to walk you through the process straightforwardly.
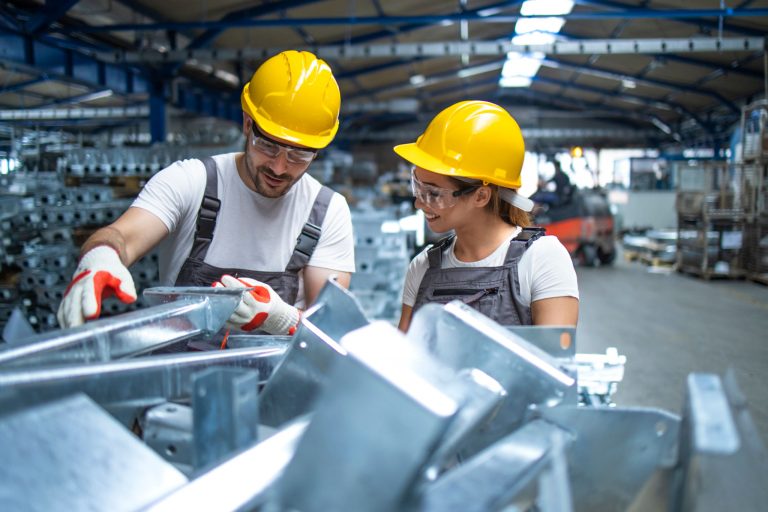
Step 1 – Choosing your metal.
What is your product’s use? How will it be used? How long do you expect it to last? How much should it cost? How quickly do you need it made? Is weight a factor? Color? Strength? There are lots of questions to ask. Don’t be overwhelmed by them. More question can help you narrow both the best material for your project and the best manufacturing processes to use. If you are able to determine both the material and the process, you will have a clearer path forward. When fabricating metal parts, it’s quite helpful to clarify your need as much as possible.
When designing the specific metal part you are trying to create, there are many considerations. In metallurgy, metals can be classified into two different categories: Soft metals and hard metals.
The most popular soft metals to use within metal fabrication are aluminum, brass, and copper. While aluminum is a highly soft metal, blending it with other elements, such as silicon, copper, magnesium, and zinc, helps create a lightweight alloy perfect for airframes, automobiles, and other consumer electronics. Magnesium is another popular light element that, when alloyed with aluminum and zinc, is especially favorable in products that require low weightage yet good strength.
The other two most popular soft metals are brass and copper. Brass, made of 70% copper and 30% zinc, is one of the most versatile soft metals, as it is extremely corrosion and weather-resistant, yet its tensile strength is almost comparable to that of mild steel. On the other hand, copper is the metal that makes electricity possible. It is highly flexible and robust while being a great electric and heat conductor.
Hard metals, on the other hand, are also essential, with steel being used in everything from trains and cars to weapons and rockets. Composed chiefly of iron, steel offers high tensile strength at a low cost while being inflammable and resisting buckling and warping. There are many different varieties of steel, ranging from carbon steel to stainless steel, each with its purpose.
Alloys such as cobalt chrome and Inconel are also perfect if you’re in the market for some sturdy and tough metals with high-performance capabilities. Inconel contains over 50% nickel, making it temperature-resistant over a wide range and quite challenging to fabricate. On the other hand, Cobalt-chrome has excellent wear resistance and human biocompatibility, making it the perfect metal for dental implants, arterial stents, and hip and knee replacements.
Some products require greater strength or harness that is available in the material alone. This can be achieved through a variety of heat treating process. Heat treating can greatly increase the life cycle of a product for certain uses. One must select the correct material and heat-treating process to achieve the desired result. A Metallurgist can help provide direction in this area. Metallurgists study and become experts in the chemical makeup of materials and effect of various heat treat processes.
Step 2 – CNC Machining
CNC or Computer Numerical Control, and the machines operated by CNC, play a vital part in the metal manufacturing industry. CNC machines help cut your raw material into the desired shape through the material removal process. CNC machinery allows for a level of efficiency and accuracy that would be impossible to replicate through manual processes. The advancements have been significant. Operations that would have been next to impossible even thirty to forty years ago, are now effortless, thanks to CNC machining. Parts can be produced in less time, with less waste, while increasing quality and lowering the chance of human error.
CNC milling machines typically utilize multi-point cutting tools. The milling machine uses a process that rotates the tool and moves it into the metal stock to remove excess material. This process utilizes the rotary cutting tools to shape the metal stock, allowing you to achieve the desired size and shape of your metal part.
Conversely, a CNC turning machine generally rotates the material and uses a singular cutting edge to remove unwanted metal from your workpiece rotates, creating a cylindrical structure in the metal part.
Step 3 – Casting and Molding.
Investment casting is one of the most well-known methods of casting. In this process, a wax mold of the final product is used. The wax is coated with a ceramic layer that is left to dry. Once the ceramic has solidified, the wax is then melted and drained. The hardened ceramic shell is a mold for the desired metal part. Molten metal then gets poured into the mold and left to cool and separate itself from the mold. This process helps ensure that detailed and complex parts can be made quickly, making it one of the most popular methods.
Die casting is another popular method of manufacturing metal parts. In this process, molten metal is poured into a steel mold under hydraulic pressure. The steel molds are shaped in a way that easily allows for complicated and intricate shapes to be made with accuracy and efficiency.
Metal Injection Molding, or MIM, is used to create metal parts when a large volume of products needs to be formed. Metal powders are mixed with polymers such as wax or polypropylene binders. These mixtures act as a ‘feedstock’ that is injected into a mold using plastic injection machines. The molded part is taken out from the mold when cooled, and then a portion of the binder is removed using solvents or catalytic processes. The result of this process is then ‘sintered’, which is a process in which the debonded product is heated to near melting point to densify the metal powders. This produces fully dense, near net-like parts that can be used in various industrial, commercial, medical, and automotive applications.
Step 4 – Metal 3D Printing.
If a metal part has too much of a complex geometry to be formed by any of the processes stated above, they are then created through Direct Metal Laser Sintering DMLS. Using a laser to fuse metals such as titanium, cobalt chrome, Inconel, or stainless steel, DMLS can form any shape imaginable. DMLS creates the metal part from the ground up, using its laser to draw thin, almost tissue-like slices of metal powder that fuse their neighbours to them when the laser passes through again. This creates a finished piece of metal with the same mechanical properties as a piece of steel emerging from a steel mill. However, some surface roughness will be present, requiring secondary polishing or machining operation.
Step 5 – Post Processing Methods.
There are three main macro-categories that post-processing steps can be divided into process-inherent, mechanical, and visual. These are applied according to the intended effect they are to have on the machined part.
Powder removal is a step that most commonly takes place on 3D printed parts. The powder that remains on the build-plate after printing must be removed. This can be achieved using routine cleaning procedures, such as brushing or wiping. The excess powder can be discarded or returned to the supplier for recycling.
Stress relief can be categorized as a process-inherent step, as it is used to relieve any stress that might have accumulated in the metal. The piece is first cooled and then heated inside a furnace and is usually performed while the metal part is typically attached to a support structure to ensure it doesn’t collapse.
Support removal is also a process-inherent step and is usually performed on 3D printed pieces. Many pieces require a support structure so that they can be printed, but these supports have to be removed before any finishing can be done to the piece. Although a bandsaw may be enough to remove support structures in most cases, in the case of stricter materials like Inconel and titanium, a CNC machine might need to be used.
Heat treatment is a mechanical post-processing step as it not only helps relieve your metal piece of any stress it may have built up but also increases the hardness, flexibility, and fatigue life of your metal. Hot Isostatic Pressing (HIP) and annealing are two of the most common heat treating processes. In the HIP, heat and pressure increase the part density and solidity, thus eliminating porosity, dealing with residual stress and enhancing the piece’s fatigue life. Annealing allows for controlling the heating and cooling processes of the metal piece, reducing stress, and allowing for improved mechanical properties such as hardness and flexibility.
Surface finishing is a visual post-processing method that optimizes the aesthetic of the metal piece, creates a smooth and polished surface, and reduces any roughness that may be left behind due to machining. Surface finishing might be carried out by bead-blasting, where tiny beads of glass or other materials are sprayed onto the machined part, making the surface smoother. Anodizing is also used to finish the surface of the metal part. The metal part is dipped into an electrolytic solution, coating it in an anodic layer that increases the part’s resistance to corrosion, and increases hardness. The metal piece may also be electro-plated, creating a protective metallic layer around the metal part.
The piece may also be colored to increase the aesthetic style of the piece and make it look much more attractive. One of the most popular methods of coloring the metal piece is to dip it into a bath of dye. This creates a uniform colored layer around the product, infiltrating the component. Painting may also be used to color the product.
A series of quality control checks will also be conducted after the product is finished to ensure that the quality is up to the mark and that the metal piece functions as it should regarding visual and mechanical properties.
Check out Greatmfg.net