Aluminum Welding Tips
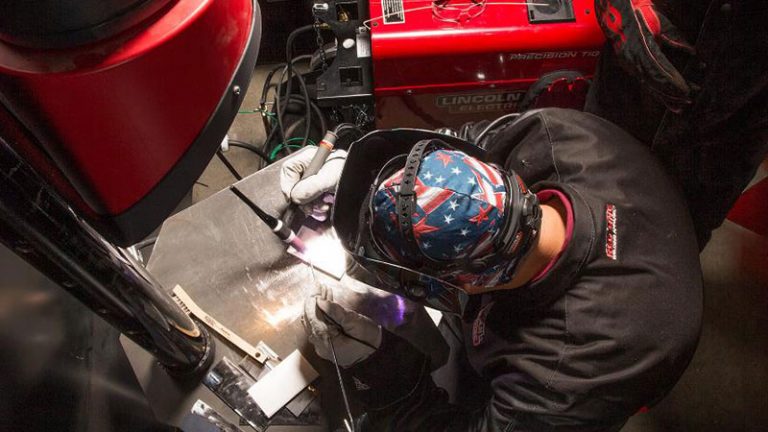
Aluminum Welding Tips
Aluminum Welding is not easy. There are two main issues when welding aluminum. The first is that the material heats up very quickly. The second is that the material has a low melting point. These two issues complicate each other. Because of this, it has been said Aluminum welding is a little like welding water. Even so, aluminum welding is a skill you can learn by investing some time and by following a few generally accepted practices. Do not expect to be an expert and have great looking welds when you start. As they say, Practice makes perfect. Some of the useful tips for welding aluminum are as follows:
One of things that many people do not anticipate is the negative impact of attempting to weld material that is not clean. Make sure the area you are welding is clean. This is very important. Even a small amount of contamination can create defective welds. Clean the aluminum by spraying the surface with a good pre-weld cleaning product. While you may not have to clean the aluminum in all areas, make sure you clean the specific areas you will be welding.
Another key step is you will want to make sure you have a strong ground all the way to your material. This is also very important. If you have a poor ground you will no doubt have difficulty when welding aluminum. You may find it beneficial to clean your ground connection area and your weld platform area.
You will need to decide if you will pre-heat the material you are going to weld. Pre-heating my not be required, but if you are going to preheat, be sure to read up on that process first. Practice on scrap or surplus material. Two most common methods of preheating are by using an oven or with a blow torch. Aluminum tends to distort quite a bit when a localized area is overly heated, such as is caused by a welding torch. Careful pre-heating of the aluminum can help to minimize the distortion. If you are going to use some form of a blow torch, be prepared to move the welding torch much faster than when heating steel or other metals. Do not stop moving the blow torch along the area to be welded, as this will cause a localized area of the aluminum stock to heat up.
What gas do you plan to use for welding aluminum? Argon gas is one product used to weld aluminum. But both argon and helium can also work depending on the equipment and used.
Aluminum can be welded with a MIG welder or a TIG welder. When it comes to equipment the general agreed standard for welding aluminum is a TIG welder. For many high production jobs, MIG welders are utilized.
Good welding equipment is nice to have when working with aluminum, but it can be expensive. In fact, a new welding power supply can easily run $6000. Top of the line equipment can run from $12,000 to $15,000 to purchase.
When TIG welding, tungsten electrodes are often used. If tungsten electrode you are using becomes contaminated, stop at once. You will either need to remove the contamination from the electrode by grinding, or select a new electrode. If you are new to TIG welding, expect to do this several times as you learn the process of aluminum welding.
When welding steel it is quite possible to fill gaps between the joining surfaces with the weld. This is a lot more difficult with aluminum welding, so all pieces must be fitted as closely together as possible. Try to eliminate all gaps if possible. Remember, well cleaned material is very helpful when you are trying to make high quality welds.
Aluminum is a low density metallic substance used in a wide range of different appliances and fields. Having such a low density is not only an attractive feature of aluminum, it excels at conducing both electricity and heat. A result of this, is it is frequently encountered in many applications that want to pull heat away from the material. This is done to prevent heat buildup or malfunction caused by overheating or even melting of wiring.
In reality aluminum welding is difficult because the material can warp, crack, bend or simply not stick. To weld aluminum safely and successfully, you need to follow these steps: Things that you need are TIG welder, Welding safety gear, stainless steel brush, argon gas supply and Heat sink. Wear a thick long sleeve shirt to prevent yourself from getting burned.
Depending on your application, you may benefit by Using a heat sink. Because of aluminum’s tendency to conduct heat very well, a heat sink can help wick away heat from the area you are welding. By clamping a heat sink to your work piece, you may be able to prevent the metal from warping or the workspace from becoming too hot to work around.
To summarize:
Clean your workpieces
Check your ground connection
Consider preheating
Use the proper equipment
Use proper safety equipment
Use a heat sink if needed
Remember these tip and practice, practice, practice. With practice, you can become proficient at aluminum welding.
Check out
Carlsonmfg.com
Great Mfg, LLC
c